
Gaines and Company Rebuilds Safety from Ground Zero to Excellence
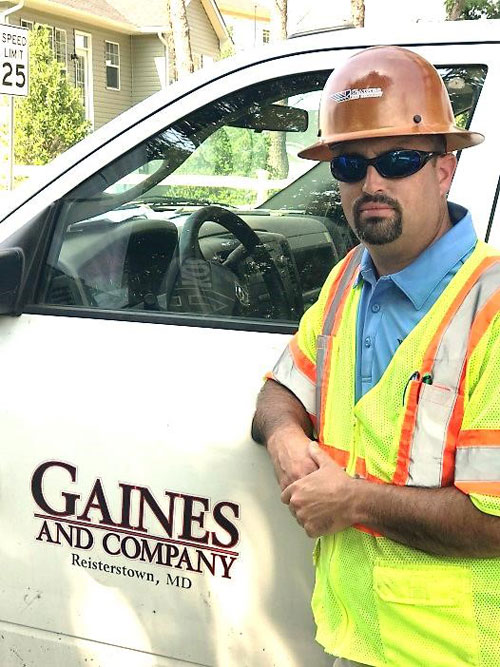
Dominic Pope, Safety Director of Gaines and Company
It took a village to do it, but Gaines and Company made the commitment to build their safety program from scratch and the results are amazing.
When Gaines and Company Safety Director Dominic Pope recommended a complete restructuring of the company’s safety program from ground zero, upper management immediately gave him the green light.
Pope, who had just been hired as a fulltime employee in 2013 after working the previous two years as a safety consultant for the turnkey site development company, intuitively knew that the current safety policies and procedures were in need of attention.
“We had safety before I came to work for Gaines and Company,” says Pope, “but it’s changed a lot, it’s really, really progressed.”
Indeed it has. The company’s Experience Modification Rate (EMR) is well below the industry average. Safety training is now a well-oiled machine. Everyone thinks about safety on and off the job, from underground utility and grading and excavating crews to the highest levels of management. So how did Gaines and Company go from being perhaps a bit blasé about safety, to it becoming a topmost priority? The answers may surprise you.
First things first, management plays a key role in safety
Pope knew he was going to need strong support from upper management in order to succeed with his safety overhaul. Lee, Myrt and David Gaines, Gaines and Company’s president and vice presidents, definitely play a “very large role” in companywide safety, according to Pope. “It’s been a growth with all of it,” he says, “but ultimately if you have people like Lee, Myrt and David in upper management that have your back and stand behind you, that makes it ten times easier.”
“Dominic’s just done a good job of getting our ear,” says VP David Gaines, “getting us all to focus on safety from the lowest level to the most senior level.”
Building a safety culture from ground zero
Pope was about to make big changes in the way everyone felt about safety at Gaines and Company and in order to do that, he had to scrap the old plan and start over. “It was a lot easier from ground zero to what we have now just trying to teach the guys what’s right and what’s wrong,” he says.
It’s a lot easier than taking an old plan and trying to recreate it – it was nice to start from ground zero.
Dominic Pope, Safety Director, Gaines and Company
…meant changing hearts and minds
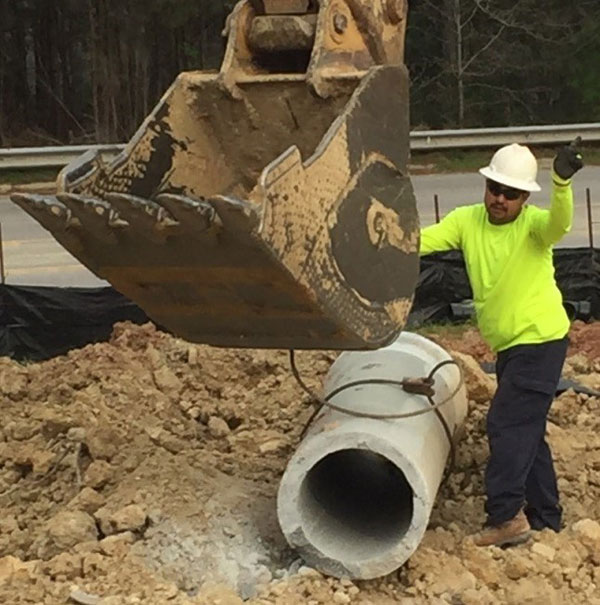

Enforce. Manage. Hold accountable. This was about to become Pope’s daily mantra. It wasn’t going to be easy to change attitudes about safety, and in order to do that he was going to have to stand tough for his principles. “It was a process,” says Pope, “You want to tell them this is how it has to be but also they have to learn to accept it. I just had to learn how to get the guys to buy into it.” That took patience, tenacity and some firm coaxing. “At first it just involved more enforcement on the guys and really just building the culture,” he says.
Positive reinforcement and trust are two big factors in Gaines and Company’s safety foundation. When asked what his biggest challenge was Pope quickly responds “really it was just getting the guys to understand the reason for safety and why we do it and not trying to be the bad guy all the time.” The learning process was a two way street. “I had to learn positive reinforcement,” Pope says while trying to teach everyone the importance of bringing safety issues to his attention.
“Everybody always wants to say the bad with safety and I’ve had to learn that you’ve got to give the good on top of it too.”
Pope acknowledges that trust is paramount. Not only did he have to gain trust around the company, he had to earn it to get across an important message. “You’ve got to get these guys to trust you, why you’re here, so you’ve got to build their trust,” he says. It didn’t happen overnight. “It took me a couple of years to get them to understand I am the middle man, the interim between the company and them,” he continues, “to let them know we’re doing this for a reason, not for the company as much as for both them and the company.”
Trust also means being respectful. In the past, Pope found that sometimes crewmembers had been embarrassed to ask him questions. He has a remedy for that. “You’ve got to help them when they need help and understand, pull them off to the side, talk to them one on one, don’t call them out in front of guys.”
Now they are recognizing hazards and bringing them to Pope’s attention. “That’s how you know you’ve won,” he says.
The generation gap is bridged
It may not seem important, especially for some of the younger millennials, but to Pope the expertise of the older generation is invaluable. He relies on the experience of management and foremen who have been in the site development contractor business for over 40 years. “I try to get the younger guys in my generation to listen to the older generation a little bit,” he advises. “That’s what I had to learn, you take what they know – the 40 years – and incorporate it into what you’re trying to phase in or change.” This means having an open mind to the wiser generation because “they’ve seen the changes I haven’t seen,” he says. “I just came into safety 8 years ago. So they’ve seen the change. You’ve got to learn from that.”

It Takes a Village
Pope humbly (and repeatedly) points out that he is not the sole reason behind the companywide safety turnaround spanning the last five years. He pays tribute to employees for taking the knowledge they’ve been taught and implementing it into their daily tasks. “Everybody will sometimes make the comment, even David or Myrt, that we do so much better since I’m here,” he explains. “I don’t think it’s me. I’m only one person. I think it’s really the guys – the credit is to them.”
He sees himself as more of a conduit of information that he doles out and readily admits it’s not worth anything unless crews take it out into the field and use it. “So it’s really the guys, just getting them to understand why we have to do it that way and giving them the tools and the things they need to know to work safely. Ultimately that’s where I’ve seen the change.”
Patience paid off with rewarding results
“Our safety record in 2017 was very, very good,” claims VP Myrt Gaines, “at least fifty percent better since Dominic’s been here.”
“Insurance companies rate you according to how many accidents you have and that’s how the insurance company bills you,” says Myrt Gaines. “It’s gotten 100% better.”
Dominic has shown us you can be safe and productive at the same time and that with a little bit of investment and time the company can get a lot better and I think we’ve seen the results of that, lowering our incidents of workers comp claims.
David Gaines, Vice President, Gaines and Company
“Guys are reporting things more freely now, they feel they have a voice,” says VP David Gaines. “I know that down in North Carolina we went to work on military bases and we didn’t have an OSHA citation for anything. We got inspected three or four times and we didn’t get a citation – not one. I think it’s been amazing.”
Safety training is a BIG deal
Safety training is what really minimizes risk at Gaines and Company and it has become a vital piece of the company’s safety infrastructure. It starts with new hire safety orientation. “Any time we get a new employee we sit them down and give them a very thorough new hire orientation,” says David Gaines.
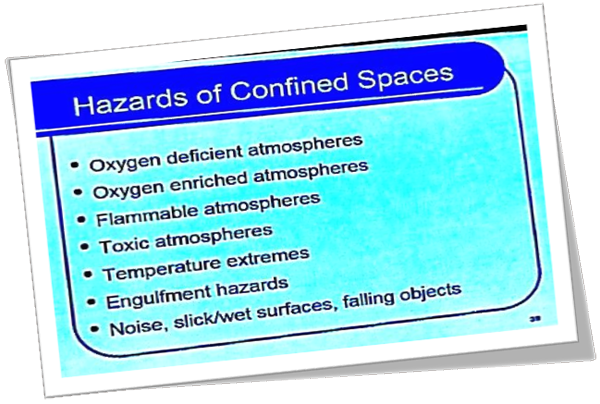
Every new hire for this site development contracting company must attend a minimum of three to four hours of training. These new employees watch a National Utility Contractors Association (NUCA) safety video that has been incorporated into the new hire process, go through company policies from required PPE to new rules that might have been put in place and added to the handbooks. “They’re going to get the handbooks explained to them,” Pope says, “copies of all that, the video takes 45 minutes to an hour then they usually spend a few hours with me.”
Training has changed over the last five years. Where in the past it was maybe a five minute talk on the jobsite or an annual course, now Pope is training on rain or bad weather days all the time.
“We hit it a little more in depth now,” he explains. “I’ll kind of pick something whether it’s OSHA 10’s or what we’re going to do in the winter or rain days so we kind of pick rain days instead of when it used to be just annual.” Pope schedules one whole day where employees take safety courses like First Aid and CPR, confined space, OSHA 10 HR or OSHA 30 HR in smaller groups, or larger if possible, depending on the weather and the time of the year. “And then you have your annual or bi-annual stuff that you have to constantly hit but it’s just more routine, just getting the guys in from new hires and keeping everything going from there,” he says.
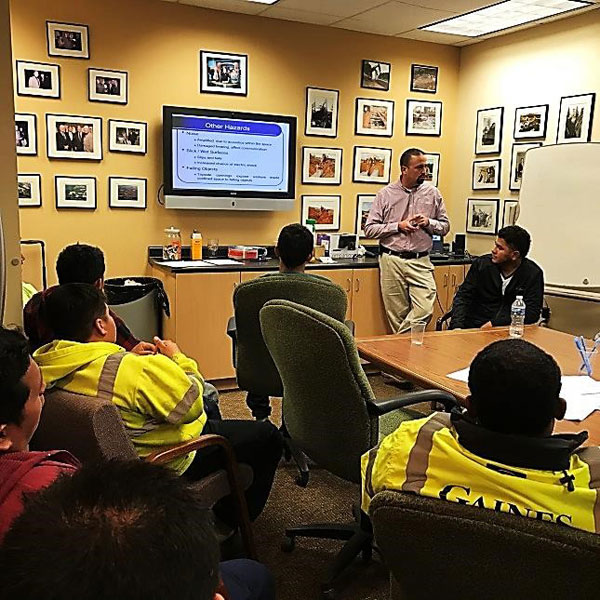
Pope holds many safety certifications, including OSHA excavation, trenching and soil mechanics and ATSSA traffic control supervisor, and does a lot of the training himself. He says the best way to teach safety is through show and tell. “I talk to them about accidents that happen in the industry, people getting severely injured or killed doing the same thing they’re doing and I bring it to their attention,” usually through weekly toolbox talks.
Safety Excellence Program
Safety at Gaines and Company could not be complete without a strong safety program. On August 1st of this year, Dominic introduced the newly minted Sportex Safety Recognition E-store, an interactive online shop where employees can use safety bucks or scratchers to earn gear like tumblers, shirts and tools. “When the guys do something above and beyond what they’re expected to do, for example turning in anything that’s damaged or bringing up safety issues, we’re going to recognize that,” he says.
Pope makes safety fun and stays ahead of the curve
So where does safety go from here now that Gaines and Company has hit their stride? There’s nothing worse than dry, boring safety. It can be difficult to get your message across to a room of bleary-eyes and yawns. “I’m always looking ahead on how to improve on what we have now,” says Pope who believes keeping safety interesting is key. With the new online Sportex recognition shop he says “I’m thinking at the beginning of next year we’re going to challenge them to something a little different. I’m going to work with upper management to figure it out.”
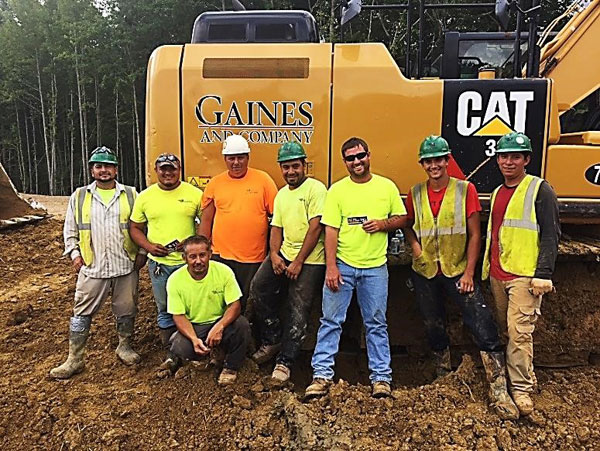
Pope has his eye on the future of safety for the company. “People can get tired of the same safety program over time,” he says, “that’s why I’m always looking for new ways to keep them involved and to make it fun.”
Dominic Pope, Safety Director, Gaines and Company oversees the safety of over 210 employees in both the Maryland and North Carolina divisions and holds many safety certifications. Pope has been the company’s central point of safety for seven years, two as a consultant and five as an employee. In 2013 he, along with management, built the company’s safety program, policies and culture from the ground up resulting in a significantly lower EMR, expert year-round safety training and admirable safety excellence. Through positive reinforcement, Pope has made everyone from employees and crew, to upper management confident that in their everyday work and activities they remain safe at all times.
Dominic Pope, Safety Director in action: https://www.youtube.com/watch?v=kvS4oR-Fojc